gt2P’s Remolten series is nominated for the 2017 Beazley Designs of the Year.
In this collection of interviews, some of this year’s Beazley Designs of the Year nominees share their design stories, challenges and aspirations.
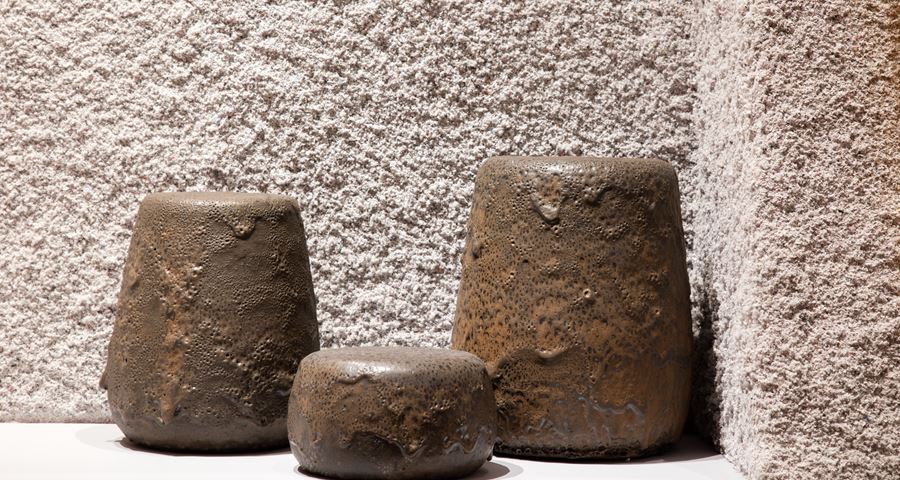
What makes good design in your opinion?
In our opinion, good design (nowadays) is the design related to design processes. When you design a process, all the involved phases turn into in a single continuous creative process. This fact gives us relevance as a designer (architects) because the control and the knowledge created to generate and produce something still belongs to the design field.
What three words would you use to describe your project?
Just in three words: Lava Paracrafting Process.
What was the first conversation you had with your team, which brought about the inception of your design?
During the making of some lights using our CPP method someone at the studio was interested in working with lava because this was part of his childhood and because a client gave us some chunks previously from the Chaiten Volcano.
By reading about the material, we realised that the lava melting point was at the temperature range in which porcelain gets strong.
After this finding, we asked ourselves: what would occur if we put together a porcelain biscuit and lava into the kiln? We supposed that the porcelain would remain solid at that temperature and the lava would turn viscous. The result was that the lava drained slowly over the solid piece of porcelain, where the shape, gravity and temperature permitted (almost like a candy). Finally, thanks to the slow cooling process, the lava contracted gradually without breaking the porcelain but holding it completely, achieving a collaborative material with zones of greater mechanical resistance within the piece.
It generated a perfect fit for the development of luminaries made by CPP system that allows us to generate very slim and reinforced pieces establishing a contrast between opacity in the hanging points and translucency over the edges where the light comes through. From this result, we started asking ourselves if lava could be a main material to be researched. (We could say that CPP Lava vs Porcelain lights are the early Remolten pieces).
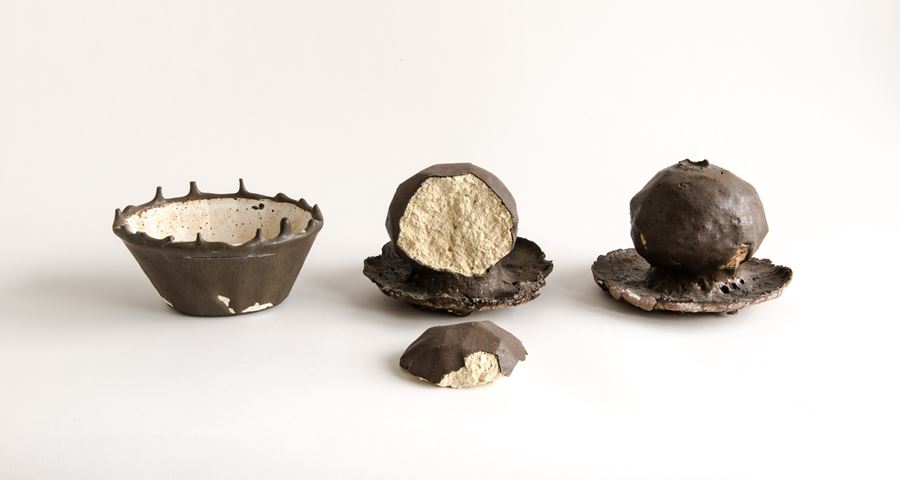
Take us through your thought process and design thinking for this project?
We have been working on the design and development of a parametric physical methodology for the production of objects made of “re-molten” Chilean volcanic lava.
Chile has the second largest and most active chain of volcanoes in the world. Throughout the Chilean mainland, there are at least 2,000 volcanoes. Of these, only 500 are considered geologically active, 60 of which have a recorded history of eruptions in the last 450 years, with a total of around 300 eruptions for that period. Currently, 43 are being monitored by the National Network of Volcano Monitoring (Red Nacional de Vigilancia Volcánica) of the Chilean National Geology and Mining Service, the most active being Villarrica, Llaima, Calbuco, Chaitén, Láscar, Michinmahuida, Nevados de Chillán, Lonquimay, Copahue, and Azul-Quizapú.
Close to volcanoes and on their slopes, we can find traces of eruptions which reveal isolated phenomena such as large rocks expelled many kilometers from the crater, and mass phenomena such as actual petrified lava rivers. Both phenomena have the same material: a large black porous and lightweight rock called basaltic andesite (Andesita Basáltica), more widely known as the “volcanic lava of the Los Andes.” This material has great potential given its extensive presence in northern and southern Chile.
Based on these facts, we asked ourselves:
What if we transform it to its original state?
What if we Re-Molten it?
These questions took us to work on “Remolten”. It is the second collaboration of the Chilean studio gt2P with the New York-based gallery Friedman Benda. It is mainly a practical research project to develop a physical parametric methodology (Paracrafting) for the production of pieces in “Remolten” volcanic lava. This project has its antecedent in the material experimentation carried out in our lighting project called “Less CPP N2: Porcelain vs Lava Lights”, which sought to increase the mechanical strength of porcelain in the firing process in conventional high-temperature kilns.
Lava from the Villarrica, Osorno, Calbuco and Chaitén volcanoes were the main raw materials, which was instrumental in obtaining the temperature parameters that allow a viscous state of the material to melt along with the porcelain, giving a viscosity range between 1200 °C to 1300 °C and achieving a greater fluidity with the latter temperature.
Then, two productive methods have been developed during this project so far:
1) Remolten Volcanic Lava Casting:
In this method, lava is ground to a granulated state and then it is pre-cast, when cold, to subsequently re-melt it in high-temperature kilns. Stamped molds made of non-meltable powder (alumina powder, graphite, fire clay) at 1300 °C are used. These are then placed in uncovered boxes made of stoneware or refractory plaster.
The structural resistance of the remolten lava is controlled by temperature curves in the furnace. This means that there is a temporal relationship between how the lava is melted down and how it is cooled. For example, in order to create a lava obsidian crystal, the rock has to be melted at very high temperatures. Then, it must be quickly cooled and tempered almost like glass. In contrast, to make a resistant rock it has to be melted at high temperature and must be slowly cooled.
The color of the lava is another aspect that can be controlled by the temperature. At 1180 °C, it is red, and the lava is joined but not melted. At 1200 °C, it is grayish black and progresses into shades of brown at 1300 °C.
Given that the pieces are heavy, solid and compact with a high thermal inertia, it allows the creation of small pieces, such as jars, plates, candleholders, wall components (tiles), and heat-resistant kitchen tools, among many other things.
2) Remolten Volcanic Lava Coating:
In this method, lava is also ground to obtain specific grain sizes, but what is different from the previous method is that the objects are coated in Volcanic Lava. The internal structure of these objects is made of materials with great resistance to high temperatures such as stoneware, porcelain, and refractory concrete.
In this case, the temperature curves also control color, resistance, and the superficial aspects of lava. We can make smooth, dripped pieces as well as completely rough pieces. This procedure allows us to make lighter and larger pieces, with greater structural resistance, such as stools, benches, tables, shelves, architectural building components, and murals, among others.
These experiences have created a great potential for volcanic lava, to be disseminated from Chile to the rest of the world, creating bridges between the academic, the artistic, the industrial and the artisanal world.
The first series that we developed was the “Remolten revolution Series”. In the nature, the lava rebuilds its surrounding landscape each time a volcano erupts. The volcanic lava covers and shapes its context, so it becomes a completely new landscape. Therefore, it is impossible to recognise the pre-existent singularities since they are destroyed and a new strong beauty has been created.
This situation made us question: What if we can recreate that phenomena but controlling it? What if we can still recognise the pre-existent nature that the lava covered with the expression of that new strong beauty?
In order to find answers to these questions, we developed the first prototypes. They belong to the “Remolten Revolution” series, with pieces created by means of a concentric revolution of an experimental nature, allowing the volcanic lava to adhere to the surfaces of stoneware with a range of slopes, and preserve the shape of the objects even after the lava covers them.
The results of this first series are controlled by using temperature curves for different lava expressions (trapelco = smooth, mahuanco = dripped, quitralco = rough). Although this is a controlled process and it can produce three different textural finishes, each piece is handmade directly with volcanic lava (without being purified or mixed with additives), which therefore makes each piece unique.
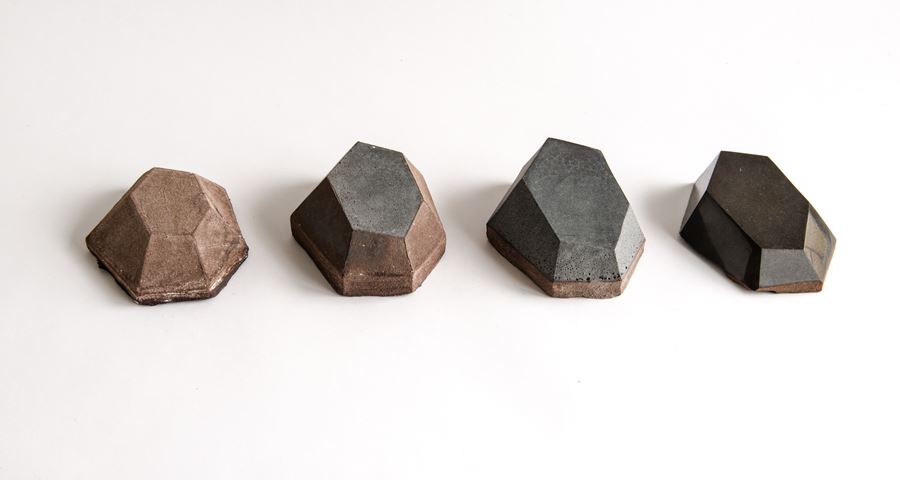
How did the subject matter influence your design approach?
Regarding the subject matter, we can say that our name “great things to People” (gt2P) is our main overarching goal, the kind of platonic goal that you never actually achieve but you are always trying to reach.
However, during the time we have worked together, we have realised that the subject matters just the same as other big ideas like sustainability and functionality. We would say they are the minimum practical parameters that a design has to accomplish, but they are not always the parameters which make you dream and create something at least own.
We don’t believe in one great idea; on the contrary, we believe in many specific ideas, apparently irrelevant, and not linked to each other, running in parallel, which in some points get intersected creating new connections and turning them into new potential projects. This is possible because we work as a team, in a collaborative way.
What obstacles did you face whilst working on your project?
In the mineral world, lava is seen as a material of little value in economic and scientific terms. Actually, when we asked some Geology professors about lava here in Chile, they repeated the same question “What do you want to use this worthless material for?” In fact, the most knowledgeable people about lava are the security experts, who study the nature and effects of eruptions as a matter of public safety. This was our starting researching point, and we joined it with some theoretical knowledge.
Another obstacle was the patience factor…. As this was a trial and error process, there were many months without “successful” results, so the resilient attitude was super important to develop this project.
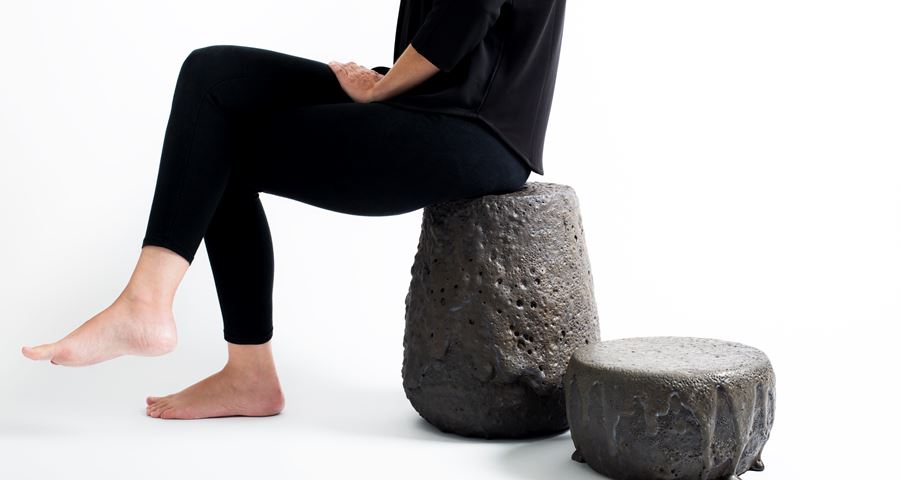
What does it mean to you to be nominated for this year’s Beazley Designs of the Year?
This nomination makes us very proud and it is extremely rewarding, due to all the effort, passion, and hard work that it has meant for the entire gt2P and our Friedman Benda gallery. We also believe this nomination also rewards all the people who believe in designing design processes, pricing the knowledge over the objects.
What’s the one thing you’d like people to remember about your design when they leave the exhibition?
That we have created a parametrical physical process that can control the Chilean Lava as a local material. It could be applied to different object typologies and creative fields, from design, jewellery to architectural features. Also, it has the potential to make alive again the Chilean ceramic industry, which has been devastated by the Chinese production.
If you had one piece of advice to a young designer, what would it be?
There are four partners, architects, in our studio and we also teach in some local Schools of Architecture and Design where we try to transmit to our students the following points, which as a whole constitute one piece of advice:
1) Think about the Process more than just about the Objects.
2) Look at your territory and your culture, and then at the world.
3) Reduce your theoretical and speculative-thought as much as you can by “Think by making”.
4) Work as a collective and build your professional network.
5) Learn from your Heroes, evaluate yourself and dream where you want to go